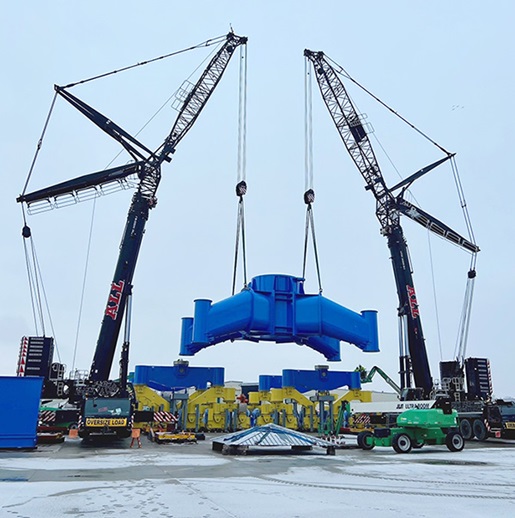
To build a crane, sometimes you need another crane or two. Especially if the final weight of that crane will be an eye-popping two million pounds.
Dawes Rigging & Crane Rental, a member of the ALL Family of Companies, is supplying cranes to help build overhead track-mounted cranes made by Finland-based Konecranes’ manufacturing plant in Wisconsin. They are bound for U.S. Navy shipyards around the world. The heavy-duty weights give them the necessary oomph to assist with dry dock repairs and maintenance to the Navy fleet.
Dawes is contracted to help build six overhead track-mounted cranes, with the potential for more. Most recently, Dawes provided two Liebherr LTM 1450 all-terrain cranes to lift and set the portal base that connects the rail wheels to the house and carbody of the crane itself. This portal alone weighs in at approximately 350,000 pounds and is 53 feet long, 25 feet wide, and 22 feet high.
Each Liebherr was configured with full counterweights of 295,400 pounds, 104 feet of main boom, and 37-foot radius at the pick point and 50-foot radius at the set point.
Because the portal is so heavy, assembly occurred right outside the steel fabricator where the part was made. It was loaded onto a special high-capacity trailer and moved to the outdoor assembly site along a dock edge on the Manitowoc River.
“Two massive cranes, a massive steel piece to lift, and the outside elements of a Wisconsin winter,” said Matthew Groh, sales representative for Dawes Rigging & Crane Rental. “It was a sight to behold.”
With each crane rigged to either side, Dawes crane operators had to move in perfect harmony to lift and set the portal. With slow and precise movements, each crane moved as a mirror image of the other. They held the portal in place for several hours while Konecranes’ personnel completed the connections between the pieces. Naval inspectors were on-site to supervise the construction process.
The high weights involved in the lift required special attention to ground bearing pressures and matting. Standard matting would be steel pads, but ground pressure on the dock wall required an additional solution, despite its concrete base and heavy pilings. Dawes brought in heavy crane timber mats and placed them under the steel pads to evenly disperse the weight.
The completed crane was loaded onto a barge right off the dock for the trip to its final destination, a winding journey through the St. Lawrence Seaway, down the Atlantic coast, through the Panama Canal, and up the Pacific coast to the Naval Base Kitsap in Seattle, where it will be placed into service.
Dawes also completed construction on a second Konecranes overhead rail-mounted crane, this one bound for Pearl Harbor in Oahu, Hawaii. Two Liebherr LTM 1450 were used for that project as well, but with different configurations, the most significant difference being the addition of luffing jibs on both. Both cranes again had full counterweights of 295,400 pounds, but 75 feet of main boom and 46-feet of luffing jib.
“Wisconsin has a rich tradition of crane construction,” said Groh. “The industry has been gone a while, but with Konecranes moving to the area a few years ago, it’s back. We’re pleased to be able to assist with that tradition.”